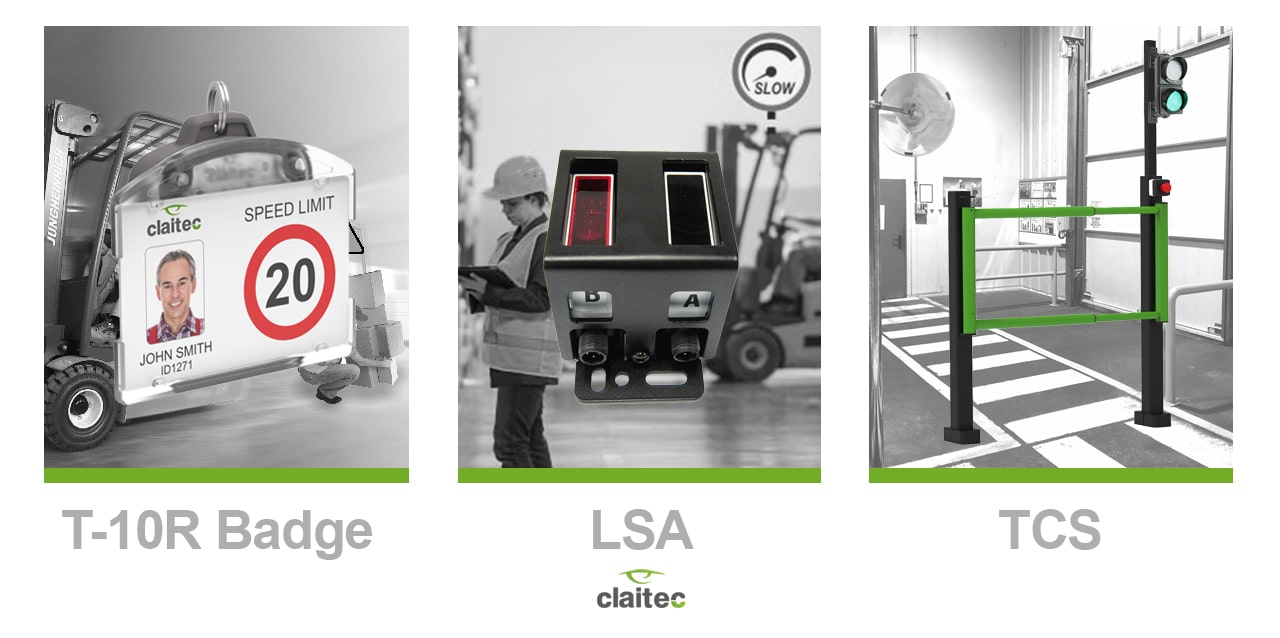
Technology delivers endless benefits to all our industries and the three tools that we will be discussing in this post are proof of it. Three valuable tools that support the different tasks performed by operators at our workspaces, protecting them from absent-mindedness or distractions and ultimately improving job safety and reducing accidents at work.
- The T-10 R Badge, an adaptation of the inventive T-10R tag with the additional feature of being a card holder. In other words, the operator only carries one single object which includes two key elements: the safety tag and the personal identification card. These help prevent errors caused by forgetfulness, loss or distraction which, in many cases are the main cause of accidents or related problems.
- The LSA Solution, an electronic safety system designed to limit the speed at which forklifts circulate. It complements the safety tools of cargo vehicles, and it reduces their speed in areas with operators or pedestrians. This solution is installed on the forklift and it automatically detects where speed limitation signals are located, generating the corresponding change in the vehicle’s gear without the need for human action, and thus protecting pedestrians and preventing accidents.
- The TCS Solution, a Traffic Control System which segregates pedestrians and forklifts in a joint workspace. The TCS System does not depend on batteries or mobile devices, and it works completely passively – it does not require human attention. The TZ2-Tag devices are installed in warehouses to detect vehicles equipped with the AC-50 Activator. Traffic lights, signal beacons, safety gates and railings are also installed to segregate pedestrians, achieving exceptionally good results in preventing accidents and improving occupational safety in industries.
Do you have any questions on this topic? On any other issue? Do you need our advice on matters pertaining to safety at work?
Don’t hesitate to contact us! We are here to help!