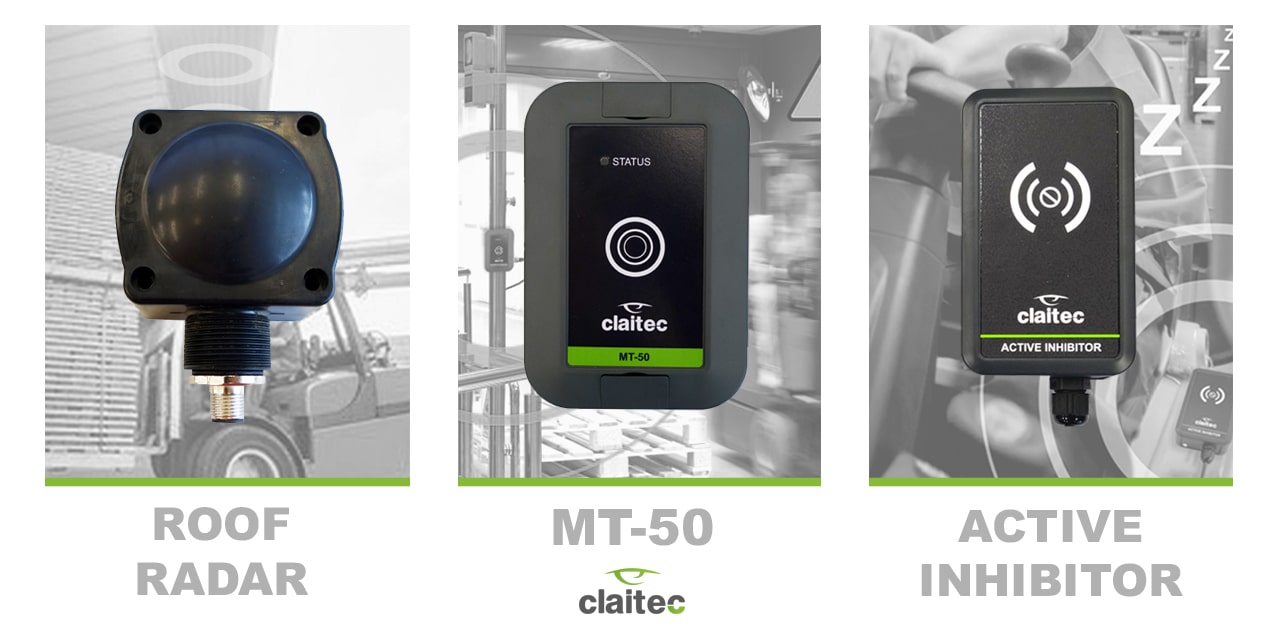
As we launch into a brand new year, there’s no better time to take stock of what 2021 left for us – a year full of emotions and challenges still marked by the impact of the pandemic throughout the world.
The collective feeling is that these have been challenging and uncertain times but we also feel they’ve brought us closer together and compelled us to work with greater confidence to add efficiency and safety to all our processes.
So, today, we would like to look back and review some of the innovative solutions Claitec developed in 2021 which are already being incorporated by our clients with great success into their work routines.
- The Roof Radar is a safety system that automatically reduces the speed of a vehicle as it enters a building. When the radar detects a ceiling, it immediately selects the low speed on the vehicle until it leaves that space again.
- The MT-50 tag is a device that bands together the functions of the TT-50, TZ-TAG, TZ2-TAG (BI/UNI). It performs the same functions of all of these did plus adding improvements in power capacity – RF and LF typical of a T-10R -, among other things. With these devices, a safety perimeter can be delimited in a physical space, without the need to have people with the T-10 key rings as was previously necessary.
- The active inhibitor consists of an electronic device that is installed next to the driver’s seat to inhibit his/her keys when entering the vehicle. This way, the drivers’ keyring is not detected and for the rest of the systems it will appear that only the forklift is circulating, thus avoiding the common crossed detections problems that tend to reduce effectiveness and pace of work.
Thanks to the trust that clients like yourself place on Claitec and thanks to the constant exchanges we have we our clients, we have thrived through another year together.
Now, it’s time to work towards an even better 2022!
Thank you, best wishes for 2022 and let’s continue facing new challenges together!